
Bamboo less is the future of the industry: Ankit Dhorajiya
Krishna International Overseas manufactures machines as per customer's need
The “Make in India” initiative has not been successful in the agarbatti industry, as 80% of manufacturing equipment still is imported from Vietnam and China. According to Ankit Dhorajiya, a Partner in Krishna International Overseas, the domestic incense automation industry is struggling to keep pace with the booming agarbatti industry. According to Ankit, the credit of introducing high productivity fully automatic machines in the industry goes to Krishna International Overseas. He also believes said that the agarbatti industry would turn to bamboo less products in the next two years. Explaining the reason for this, he said that bamboo, the main component used in incense sticks, is still dependent on China and Vietnam. The bamboo produced in India cannot yet meet the needs of the industry. Along with this, for the last few years, a part of population is restraining from burning of bamboo in incense sticks. In such a situation, the market of non-bamboo products such as Dry Stick, Dhoop Cone and Sambrani Cup is growing rapidly. Therefore, as per to the need of the market, the dependence on machines will increase to produce such products. Apart from this, from past 1 year, the company is also manufacturing bamboo-less products, which are smokeless and under the guidelines of The International Fragrance Association and act as room fresheners. The company exports these products to 18 countries mainly through Amazon.
Ankit Dorajia told Sugandh India that Krishna International Overseas was established in 2017 and he has been associated with the group since 2012. Earlier he was Marketing Manager in the company for about 10 years. Later in 2020, he became the partner of the company. He said that Krishna International Overseas manufactures machines for making and packing incense sticks, dry dhoop, Sambrani sticks, cones and sambrani cups. The company also manufactures backflow cones and other bamboo less products for export. The company also has its own export brand of bamboo-less products. He told that before designing a machine, we do a lot of research. For example, earlier there was no fully automatic machine to produce dhoop sticks ,all the work had to be done through manual labour. Manufacturers want greater production and the shortage of labour is a major issue. Understanding these issues, we started producing full automatic machines, in which there is automatic feeding and automatically dhoop sticks come out in the tray. After this we made a cone making machine. For this, we researched the market and found that the machines available produce only 150 kgs, but there was a demand for 500-600 kgs from the manufacturers. In such a situation, the manufacturers had to increase the number of machines along with more workforce to run them. We acknowledged this and made the biggest machine which has the capacity to make 500-600 kg cones. This machine produces 1800 cones in 1 minute.
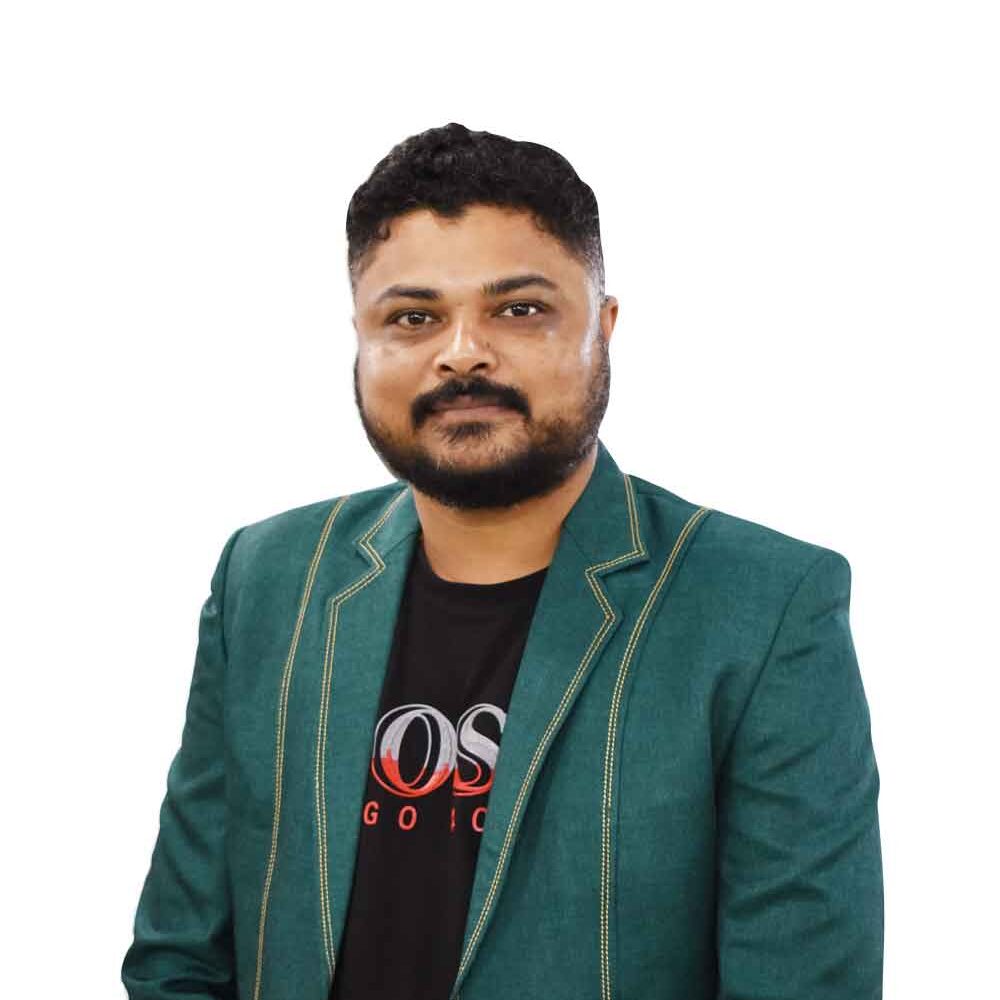
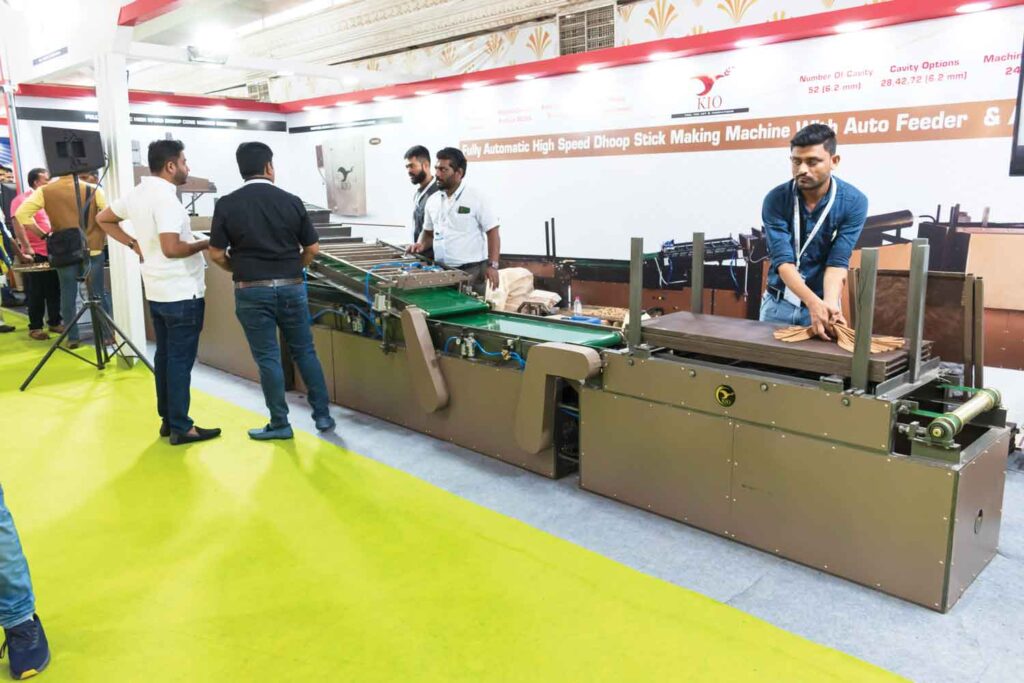
There has been a boom in Sambrani Cup market. Ankit informed that despite having machines, there was still a lot of manual labour work that had to be done. From pouring the ingredients into the machine then furthing pouring the spice into the cup, everything needed to be done manually. We designed a machine in which the ingredients need to be put in the machine and the machine does everything from making the cup to filling it with ingredients and further stacking it up in the tray, ready for drying. Similarly, manufacturers had to use separate machines for packing and weighing or counting incense sticks and dhoop. We realized this and designed a single machine that can weigh/count and pack incense sticks, dhoop, cones, dry sticks. It also takes less space compared to multiple machines.
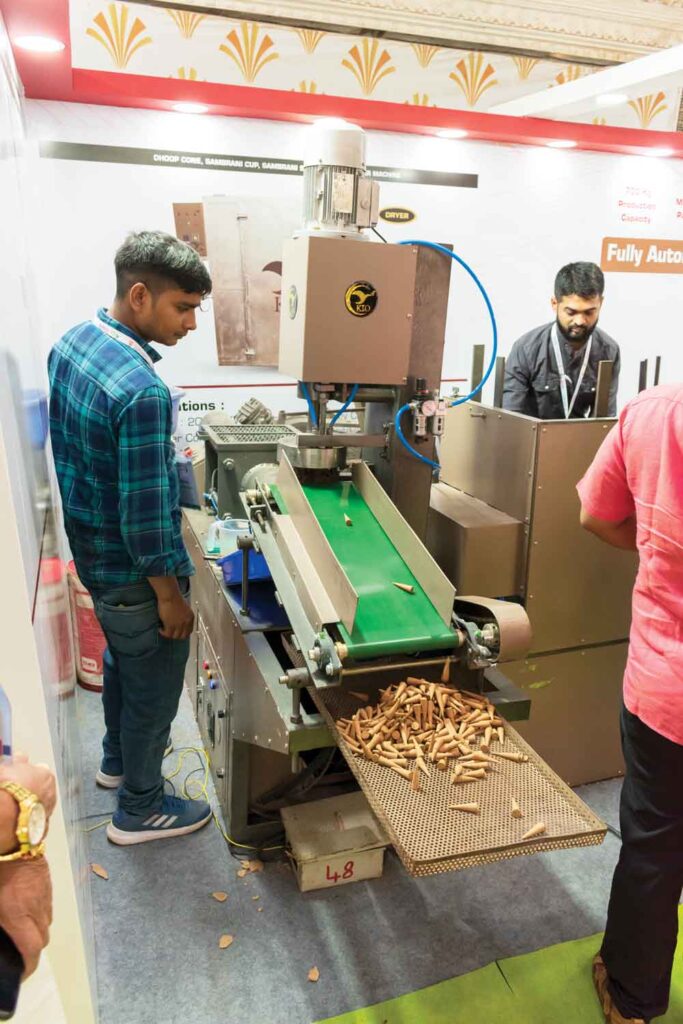
Informing Sugandh India about the incense sticks making machines, Ankit said that good quality incense sticks should be uniform.The handle and coating area should uniform too. He told that the company has “6GPro” machine for making incense sticks. It is mostly for export and has been exported to many countries. The company’s engineers personally go there and install the machine. This machine has been the choice of some manufacturers in India as well. The quality of incense sticks stays the same in this as compared to other machines in the market along with 25-30 percent more production. The speed of imported machine is 180-240 sticks per minute while the speed of our machine is 300-320 sticks per minute. The hardware and motor speed in the machine are optimally designed, so that the machine does not malfunction even after maximum production. Apart from this, branded parts are fitted in our machines and they are available everywhere. Therefore, the manufacturer does not face any problem in getting the parts or servicing the machine. He can buy them from anywhere. Ankit told that we have done R&D on machines with higher speed than 6G Pro version. High speed machine producing 400 sticks per minute. Such machines have been installed by 10 to 12 manufacturers in the country, but they aren’t used much. The industry is not yet ready for this, because for that the bamboo stick should be of the best quality. Only then will it run successfully. He told that the company has made 6G eco machine for economy product. That too is of better quality than the machines coming from Vietnam. The Vietnam machine produces 50-60 kg, while our 6G eco can produce 70-80 kg. Its speed is 260-280 sticks per minute.
Informing about machines for dhoop sticks Ankit said that he has a wide variety. The difference is based on the cavity. In this, if the diameter of the dye of 6 mm is taken, then the machines can be categorized into 28, 42, 52 and 72 lines. Generally, manufacturers prefer the 52 lines model. Further, there are different versions, one has manual feeding and collection, second has automatic feeding and collection manual and third has both feeding and collection automatic. 95% of the machines we sell are of high automation as most of the manufacturers want less dependency on labour.
For Sambrani cup making machine, Ankit told that after a lot of research on Sambrani cup, we made a machine of 20 cups Stroke. It produces 3-4 thousand cups per day, but we further innovated it and increased the speed which increased the production to 6 to 7 thousand cups. Then, we made a version of 40 cups per Stroke, which can produce 14 to 16 thousand cups per day. We further introduced more automation in this and made a version of 50 cups per Stroke which can produce 72000 cups per day. We also added the feature of automatically filling the cavity with material and along with the feature of automatic tray collection and furhter added the feature of automatic filling of ingredient in the cups. Recently we have also designed 72 cups per Stroke machine. The cup making and cup filling material is to be fed into the machine and the rest of the work of cup forming, filling the material into the cup, setting the cup in the tray for drying is all automatic. In this way the entire production has become fully automatic and the machine will run nonstop. He said that these are for premium quality products. There is also an economy model of the machine and orders for it have started coming in. He told that it has 40 cavity with a production capacity of 14000 to 16000 cups and costs of 3.5 lakh. Adding one and a half lakh rupees more to this and the capacity can be increased to 45000 cups. This design was launched 4 months back.
Ankit commented that the cost of raw material, packaging, labor charge in incense sticks and incense industry is increasing day by day and manufacturers will have to do full automation of their industry to reduce the cost. We have automated the cup production process. Our premium machines are doing better. The starting price of premium agarbatti machines is 1 lakh 40 thousand rupees and for economy, machines can be made for ₹ 85000. For Dhoop Cones, we have machines ranging from Rs 3 lakh 25 thousand to Rs 7.5 lakh. Their production capacity is up to 200-500 kg. Their speed is 600 cones per minute. Highlighting an issue, Ankit said that the cone after coming out of machine, falls and gets deformed. We have found a solution for that too. This will definitely increase the electricity bill, but the quality will be better. For producing dhoop stick, We have machine in economy range worth three and a half lakh rupees. Tray feeding is manual in this but the production of 150 kg per day can be easily achieved. Ankit confidently said that the company’s full focus is on bamboo less products, as there is a problem of bamboo in incense sticks and also all the raw material for dhoop is available in India. That’s why the industry is slowly moving towards bamboo less.

On the issues in the mechanization process of the industry, Ankit said that we have to make new discoveries every day. We design according to the needs of the manufacturers. We cannot work only for profit. We also have to look at our customer’s satisfaction and requirement. For this, we do extensive research and give it to the consumer only after we personally are satisfied. He said that at present they have no competition with any other company as we make machines as per the demand of the consumer. He said that at present out of all the machines being used in incense industry in India only 20% machines are from domestic machine makers like us. The reason for this is that people have become accustomed to the machines from Vietnam and they have full knowledge about it. However, we don’t just provide machines but also information regarding all the requirements such as raw material, packaging, etc to run a business in agarbatti industry to new comers.
Ankit said that the company is also exporting machines, but it is very limited. Only countries like Sri Lanka, Egypt, Malaysia ,Turkey demand it. European and other developed countries find it cheaper to sell imported products. He said that the from installation of machines to complete training and time to time service, we provide all the services to our clients. We provide a 1-year warranty, but even after that we make sure that the client doesn’t run into issues. This is also a reason we are not able to produce machines on a large scale, because our maximum staff is engaged in providing service.
In the end Sugandh India asked Ankit, being a machine manufacturer, what motivated him to produce products of his own? Ankit replied that people were firm that bamboo less products cannot be made by machines and so we took this challenge and designed machines that can produce bamboo-less products. Apart from this, our export clients also started demanding readymade products. That’s why we are producing since last 1-year. Our products are of the best quality and we use natural raw materials. The chemicals and fragrances we use are based on the IFRA guidelines. Our products are like air freshener. They do not emit smoke and users do not feel suffocated or cough. Ankit informed that they have 20 products in Bamboo less and 20 more in Backflow type of products. We have also innovated fragrances, including Dragon Blood, Palo Santo, White Sage, etc. that are more preferred in foreign markets. People in foreign countries like the aroma of spices. The company is sending its finished products to 18 countries through Amazon.
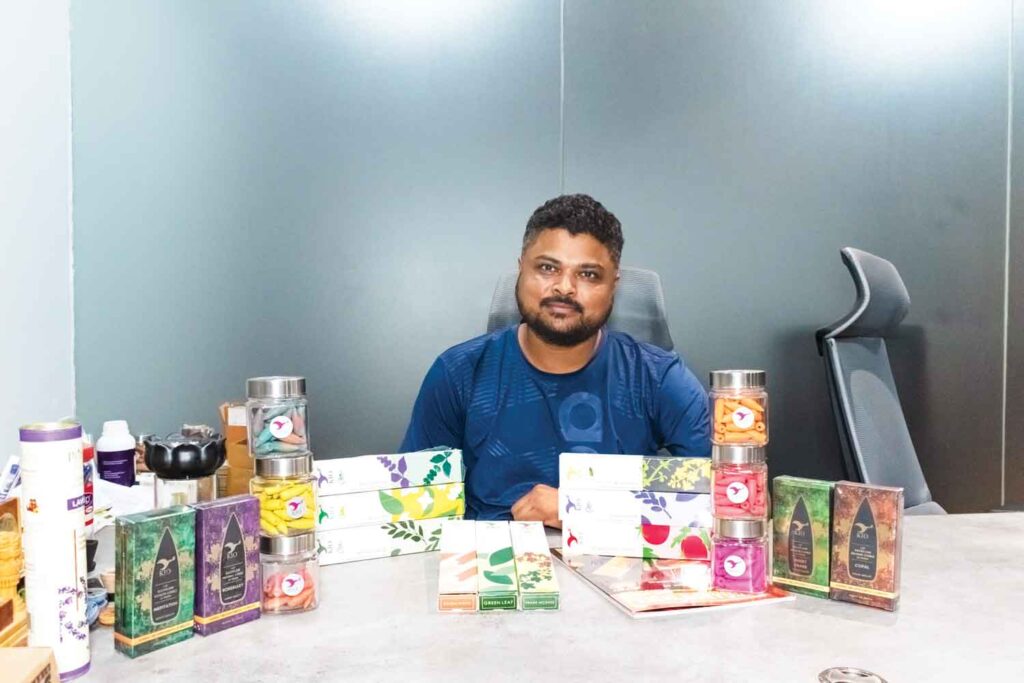